Fasteners and Machining: Integrating Accuracy and Strength in Manufacturing
Fasteners and Machining: Integrating Accuracy and Strength in Manufacturing
Blog Article
Understanding the Art of Bolts and Machining: Technologies and Ideal Practices
In the realm of commercial production and design, the proficiency of bolts and machining is a cornerstone of ensuring architectural integrity, capability, and durability in various applications. As innovation breakthroughs and needs for performance and accuracy increase, remaining abreast of the most up to date innovations and finest methods in fastening and machining ends up being vital. From the evolution of securing technologies to the intricacies of choosing one of the most appropriate materials, the landscape of contemporary production is continually advancing. Join us as we explore the current advancements and explore the nuanced globe of mastering bolts and machining, discovering essential understandings and techniques that can elevate your strategy to design services.
Evolution of Attachment Technologies
Throughout the commercial change and into the modern-day period, the development of securing innovations has actually been noted by continuous advancements in efficiency and integrity. Fasteners, such as screws, rivets, and screws, play a vital duty in various sectors, consisting of vehicle, aerospace, construction, and electronic devices. The demand for more powerful, more long lasting, and easier-to-install fastening options has actually driven innovation in the field.
One substantial advancement has actually been the change towards precision machining strategies to develop bolts with higher resistances and superior efficiency. This change has allowed suppliers to generate bolts that meet rigorous quality standards and offer enhanced resistance to corrosion and exhaustion.
Furthermore, the intro of advanced materials, such as titanium alloys and compounds, has transformed the capacities of fasteners. Fasteners and Machining. These products provide phenomenal strength-to-weight ratios, making them optimal for applications where minimizing weight is critical without jeopardizing structural honesty
Innovations in Machining Approaches
In the world of commercial manufacturing, the constant development of machining approaches has led the means for unmatched precision and performance in the manufacturing of bolts. This precise control allows makers to produce complex and complex bolt layouts with ease.
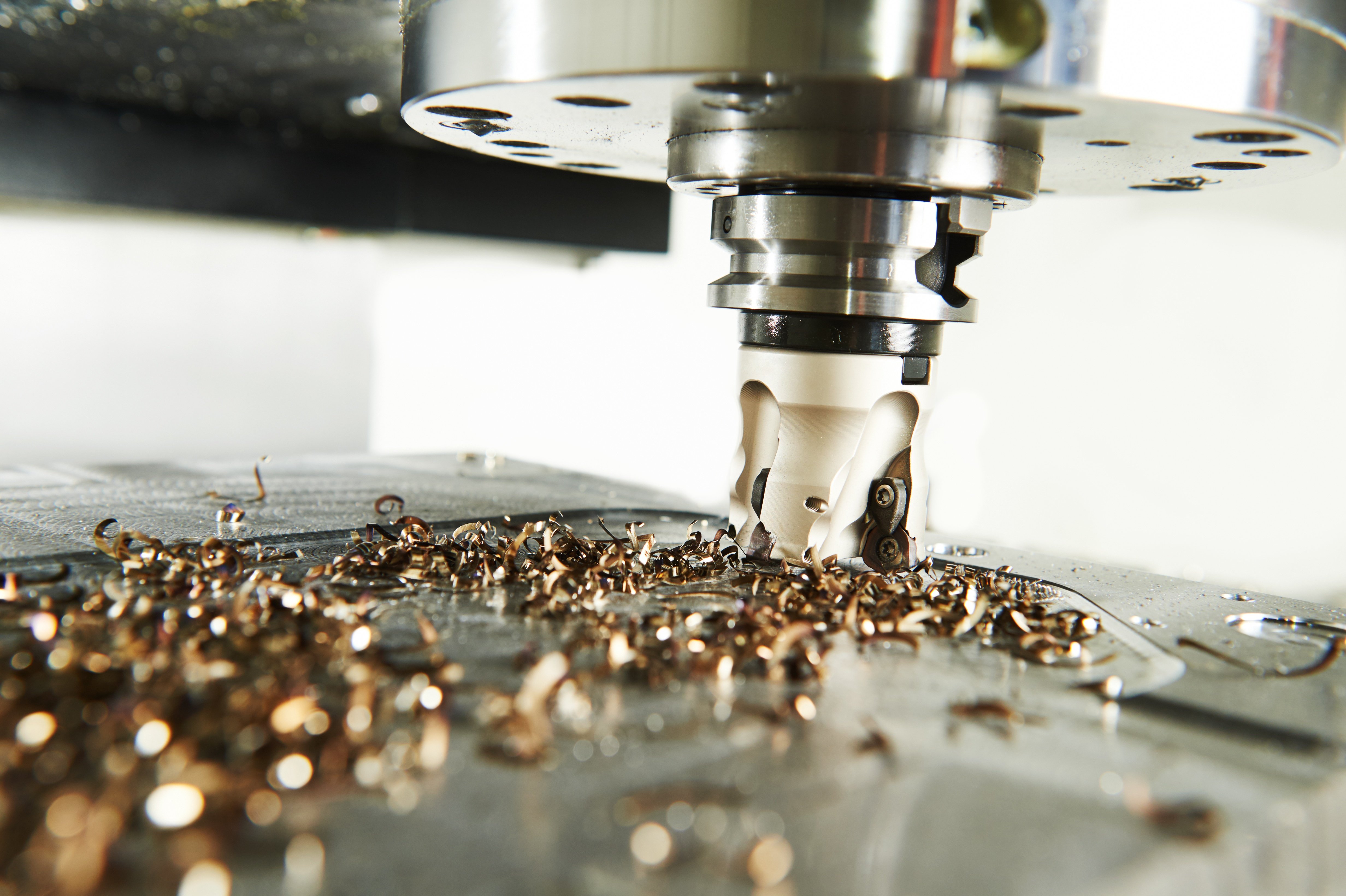
In addition, the adoption of multi-axis machining facilities has actually allowed synchronised reducing operations from different angles, even more enhancing performance and reducing manufacturing times. By utilizing these innovative machining techniques, makers can satisfy the enhancing demand for top notch fasteners while maintaining cost-effectiveness in their operations.
Choosing the Right Bolt Products
Choosing the ideal product for fasteners is a critical decision that considerably influences the efficiency and durability of the assembled elements. When picking the ideal bolt product, several aspects must be taken into consideration to ensure the sturdiness and integrity of the end product. The material see page chosen should be compatible with the ecological conditions the bolts will be revealed to, such as temperature level variations, dampness degrees, and destructive elements.
Typical products made use of for fasteners include stainless-steel, carbon titanium, light weight aluminum, and steel, each offering one-of-a-kind residential or commercial properties that fit various applications. Stainless-steel, as an example, is known for its rust resistance, making it perfect for outside or aquatic atmospheres. Carbon steel is an economical choice suitable for many general-purpose applications. see it here Aluminum is lightweight and typically utilized in industries where weight is an essential aspect. Titanium, on the various other hand, is extremely strong and corrosion-resistant, making it ideal for high-performance applications.
Enhancing Accuracy in Machining
Achieving optimum accuracy in machining is essential for ensuring the quality and efficiency of machined elements. Precision in machining describes the capability to consistently create parts within limited tolerances and with high accuracy. To enhance accuracy in machining, makers utilize a selection of advanced techniques and modern technologies. One key approach is utilizing Computer system Numerical Control (CNC) makers, which provide superior accuracy and repeatability compared to standard hands-on machining methods. CNC makers are programmable and can implement complex machining operations with minimal human intervention, causing higher accuracy degrees.
In enhancement to CNC machining, the use of advanced cutting tools and device holders can also dramatically boost accuracy. By prioritizing precision in machining, suppliers can accomplish remarkable item quality, tighter resistances, and enhanced total efficiency of machined parts.
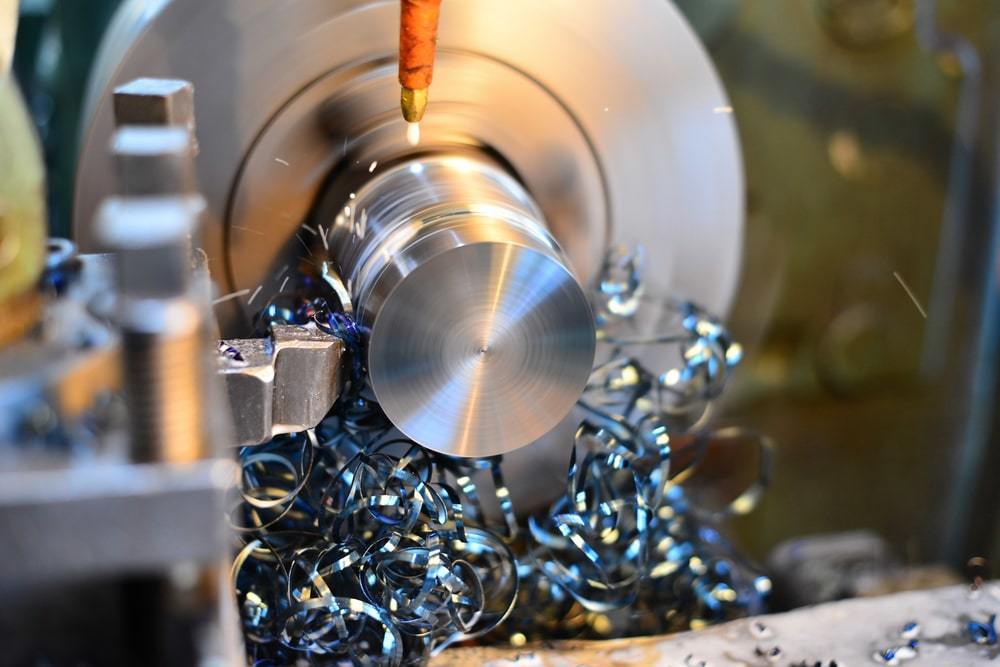
Best Practices for Fastener Installation
Accuracy in machining plays an essential duty in guaranteeing the integrity and durability of fastener setups. One key element is the appropriate selection of fasteners based on the specific application requirements when it comes to ideal practices for fastener setup. Making use this link use of the proper type, dimension, and product of bolt is necessary to ensure ideal efficiency and sturdiness. Fasteners and Machining. In addition, it is vital to adhere to supplier standards and recommended torque values throughout the installment procedure to avoid over-tightening or under-tightening, which can cause premature fastener failing.
Furthermore, guaranteeing that the fastener threads are complimentary and tidy of particles prior to installment is important to attaining a safe and reliable link. Using thread-locking compounds or washing machines can also boost the stability of the bolt assembly. Routine inspections and upkeep of bolts post-installation are recommended to determine any type of possible issues early and protect against pricey fixings or replacements in the future. By adhering to these ideal techniques, makers can maximize the stability and efficiency of their bolt installments.
Verdict
By picking the ideal bolt materials and enhancing precision in machining, manufacturers can achieve optimal outcomes in their procedures. In general, grasping the art of bolts and machining entails constant development and adherence to ideal practices.
In the world of commercial manufacturing, the continual advancement of machining approaches has led the method for unmatched precision and efficiency in the manufacturing of bolts.Accuracy in machining plays a critical function in ensuring the reliability and durability of fastener installments. When it comes to finest techniques for bolt installation, one crucial facet is the correct option of fasteners based on the particular application needs. By selecting the right fastener products and enhancing precision in machining, makers can accomplish optimum results in their operations. In general, mastering the art of bolts and machining involves constant innovation and adherence to ideal methods.
Report this page